3D Case Study | Make Small Defects Everywhere Visible
Lithium battery weld defect size detection
Testing requirement
1. Check for defects such as dents and explosion points on the battery casing after welding, 002. Check the gap width and height difference in the four directions on both sides of the shell.
Detection difficulty
01. There are many types of defects and their positions are random, which require high detection speed and continuity
02. The welds and defects are small, and the measuring equipment must have high resolution and high precision03. The battery casing has complex surface characteristics such as high brightness, high reflectivity, and high folding degree, which can easily cause interference
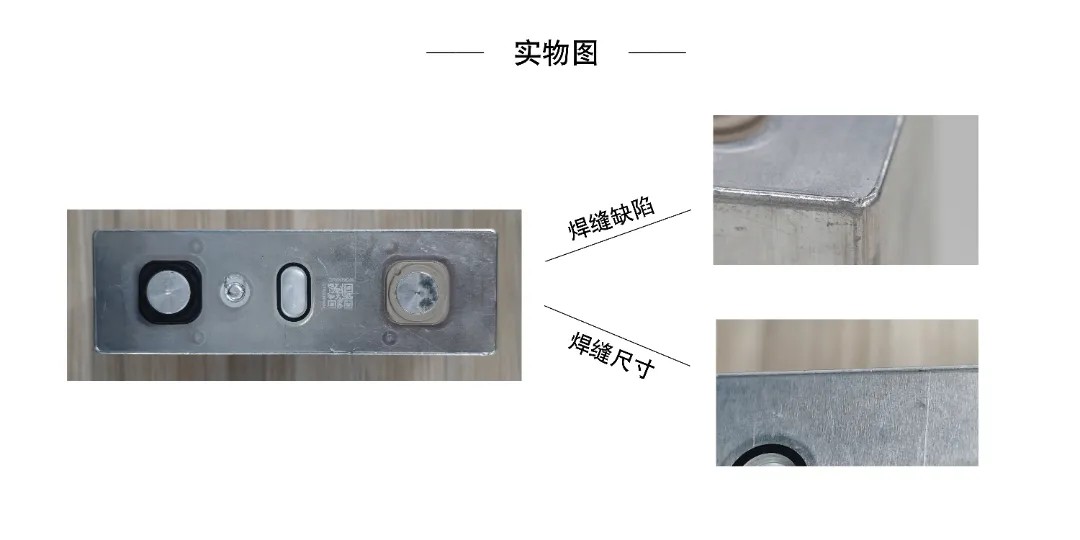
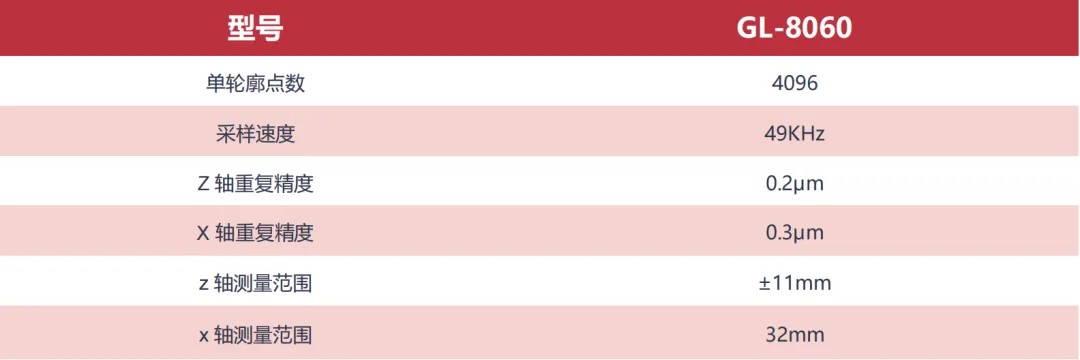
Professional optical system, micrometer level measurement accuracy, with up to 4096 contour points
△ Ultra high speed sampling 49000 contours/second
Equipped with a large aperture detection lens and an ultra wide X-axis field of view, it can achieve high-resolution 3D imaging of small welds. 00Equipped with HDR high dynamic range scanning, it can greatly eliminate noise interference and is not limited by the shape or material of the workpiece.
1. Battery weld defect detection
Tilt the camera by 30 degrees according to the product; Scan the R corner position of the product for defect detection.
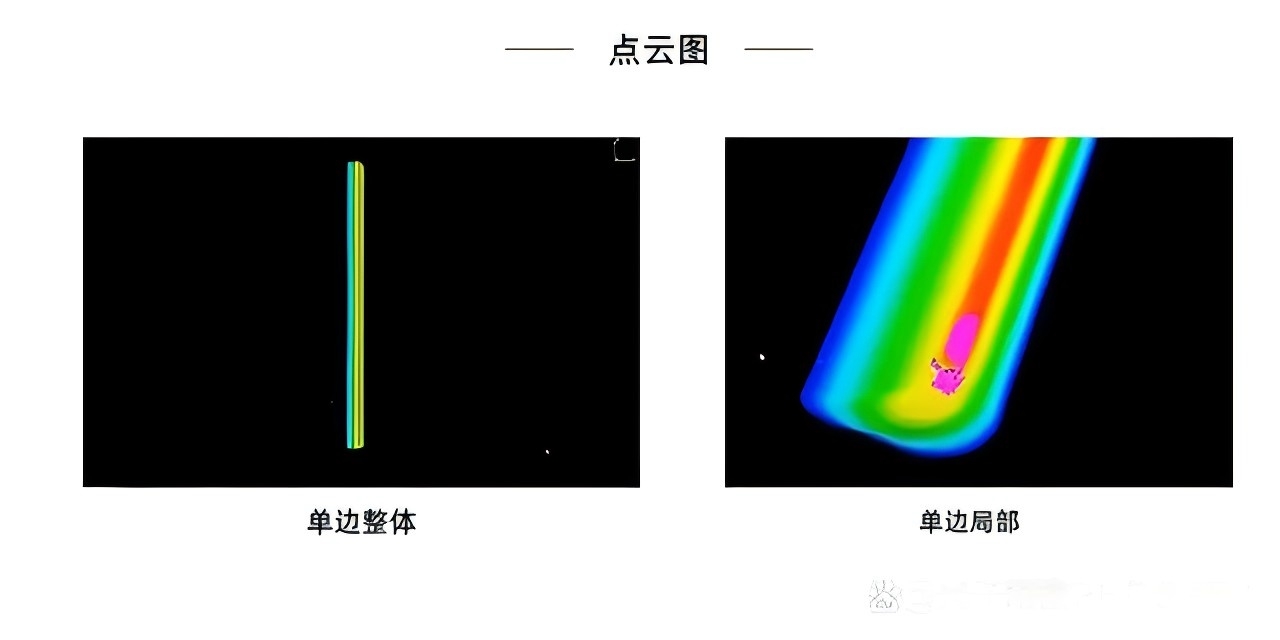
2. Battery weld size inspection
Scan the product's R angle position horizontally with the product camera for size detection. Detect the width and height difference of the weld seam. (The image on the right is a height difference detection image, and the purple matrix and orange matrix are used to calculate the height difference)
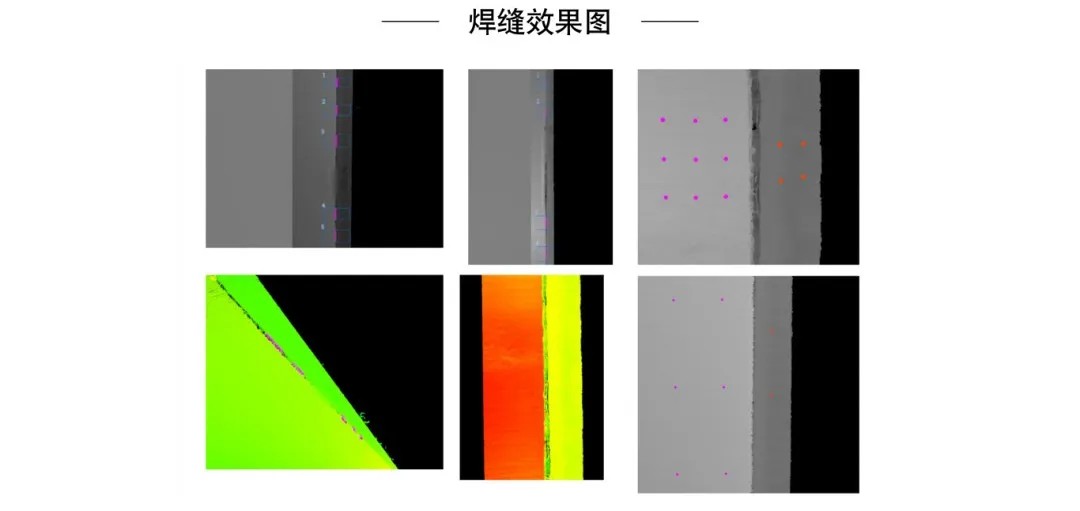
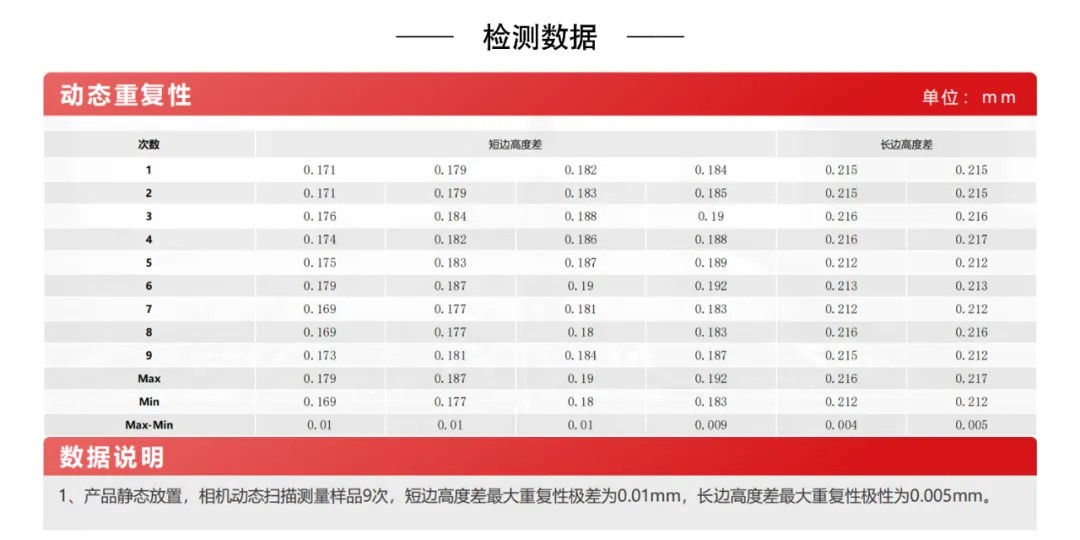