D Case Multi-camerator splicing detection opens 360 ° new horizon
In the high-speed production line, it is often necessary to conduct comprehensive appearance inspection on the workpiece in a very short time, such as: cable diameter and straightness inspection, lithium battery appearance defect inspection, rail section size inspection, etc.
This requires the sensor to completely restore the cross-sectional contour shape of the article under test and obtain accurate cross-sectional contour data. However, the detection range and accuracy of a single camera are limited, so it is difficult to obtain complete and accurate appearance information.
360°
Splicing inspection scheme
Test case: dimension of dissimilar parts&defect detection
▪ Workpiece size: 30mm * 160mm
▪ Detection accuracy: 0.5mm
▪ Movement mode: measure by moving forward and backward
▪ Inspection items: 1. Section dimension inspection
Scratch, concave-convex and other defects
Solutions to:
Four cameras laser axis tilt scanning, two-to-two calibration with a chessboard grid (camera 1&camera 2, camera 2&camera 3, camera 3&camera 4) to splice the data from different cameras into a complete 3D model of the steel pipe to achieve 360 ° 3D dimensional inspection.
▪ Machine model: GL-8060
▪ Measuring range: 62 ± 11mm (Z-axis) 29-35mm (X-axis)
▪ Number of contour points: 4096 points
▪ Linear accuracy: ± 0.03% of F.S
▪ Repetition accuracy: 0.2 μ m
▪ Sampling speed: 4KHz-49KHz
01 Dimension inspection
The full and high-precision 3D point cloud model is obtained through the around view splicing of the local point cloud collected by the four cameras, and the accurate data is obtained by extracting the key points.
02 defect detection
More depth information, such as defect size and shape, is extracted from high-quality point cloud to help judge quality defects. Defects such as bump, dent and scratch on workpiece surface can be effectively detected.
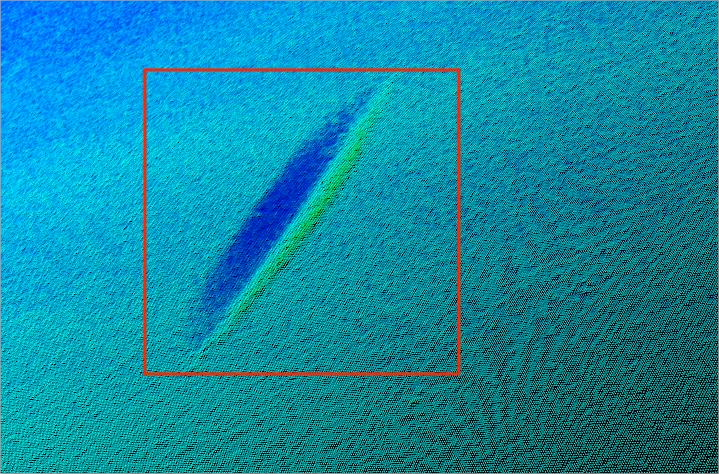
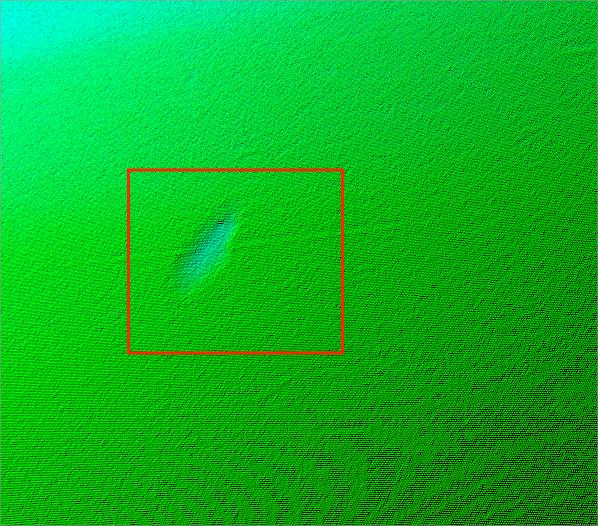